Industrial Lighting Products Compared
- Gerard Lynch
- Jan 12, 2016
- 2 min read
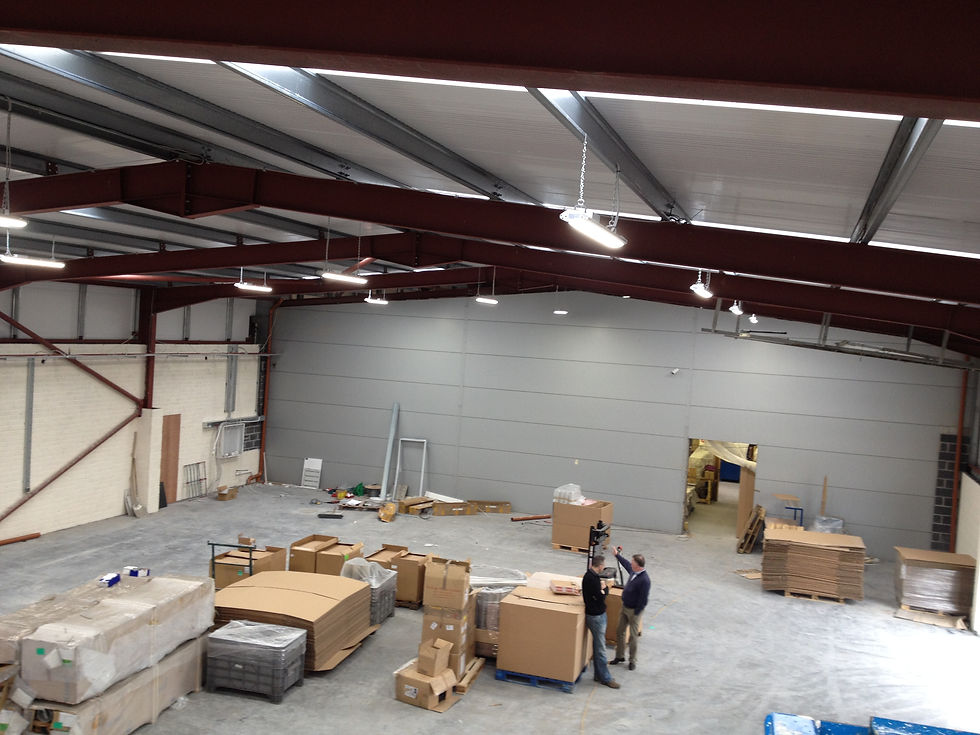
HID Lamps and Linear Fluorescents
Nearly all Industrial Facilities, more than 2 years old, use some form of HID or Fluorescent Lighting. These fittings can be inexpensive to buy and were an excellent solution in their time, however that time has now past. The problem begins with the maintenance, High Bay fittings are often inaccessible and depending on their location can lead to down time while tubes and ballasts are repaired and replaced. The last thing a manufacturing plant wants is production to be held up because lighting has failed. In many cases scaffolding and hoist have to be hired just to change a lamp! Another issue is that all these fittings emit heat. Heat, in the case of most fluorescents, means that the fittings become brittle and clips break off requiring the complete fitting to be replaced, it is also a fire and safety risk. In some industrial environments these fittings can also be a trap for oil or moisture that is in the air. When ballast fails you need a qualified electrician to go up on a hoist or scaffolding to replace them, this is an expensive use of an electrician’s time.
Next up is the running costs. Although they may be inexpensive to purchase the cost of running a Fluorescent or HID lamp is expensive. Essentially these fittings are heat sources and light is just a by-product, as we all know generating heat through electricity is an expensive process.
LED Fittings
The design and technology behind LED High Bays and Linear light fittings has moved on so quickly in the last two years, that there are now excellent solutions available for new build and retro fit Industrial Units. LEDs now have a much increased lumen output and because they consume much less electricity they are a far more efficient solution. LED produces much less heat and therefore a typical HID 400W can be easily replace by a 150W LED reducing consumption by over 60%. In addition to the technological advances increased take up of LEDs has led to a considerable reduction in cost. This means that the ROI on retro fits can be as low as 6 months and that new builds can be confident that they are installing an energy efficient product at a reasonable cost.
When we look at the maintenance costs then we see a completely different scenario from HIDs and Fluorescents. LEDs have a long life typically 5 years and this can be as long as 10 depending on usage. They generate very little heat so you don’t have the issue of parts becoming brittle. There are no ballasts or tubes to be replaced so no hoists or scaffolding is required. Industry has the comfort of being able to calculate when the lighting will next need replacing and is free from shut downs to replace tubes and ballasts. Electricians can be more gainfully employed and the facility will have one less headache for management.
Of course the financial gains in energy, maintenance and labour costs go straight onto the bottom line.
If you require any further information or would like to have a Walk Through Audit of your facility contact Gerry +353 65 41722
Comments